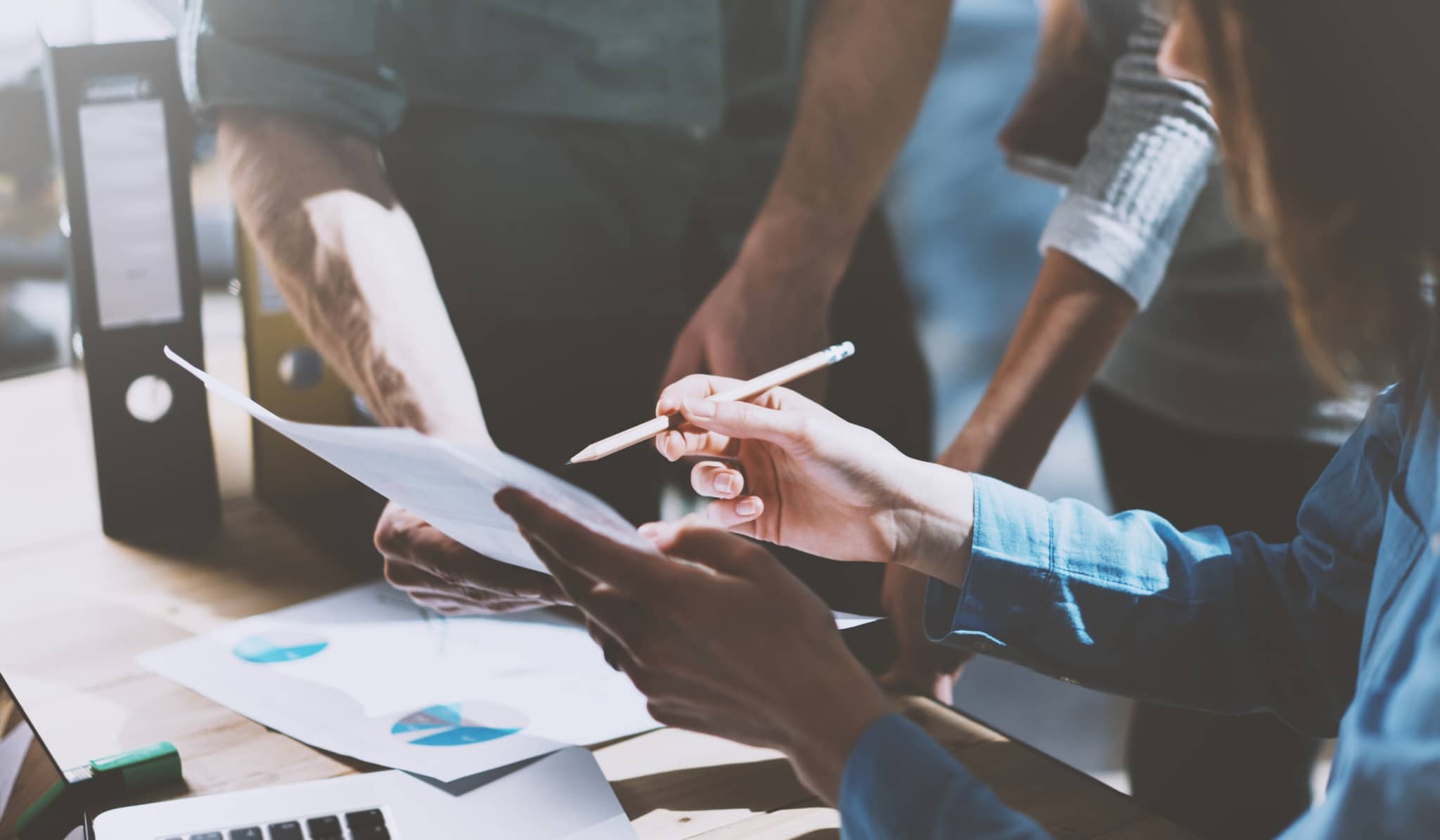
Dans “lean management”, le terme “lean” se traduit par “maigre”. S’en tenir à cette traduction littérale serait peu flatteur, voire réducteur pour une méthode de gestion si riche et si complexe ! Au-delà de la volonté de réduire les coûts et les délais, l’objectif du lean est d’adresser les véritables défis auxquels les salariés de l’entreprise font face.
Retournons alors dans les années 1950, berceau du lean management et passons en revue les principes sur lesquels il s’appuie pour ensuite déterminer si ce mode de gestion est, comme certains semblent le penser, un modèle dépassé.
Quelques mots sur le lean management
Issu de TPS (Toyota Production System), le lean management a été initié par Taiichi Ohno au Japon. Il repose sur un système particulièrement efficace dont les deux bases sont : le respect de l’individu et l’amélioration continue.
Les principes fondamentaux de la philosophie lean management peuvent être résumés ainsi :
- Placer le client au centre de l’entreprise
- Identifier et réduire les gaspillages
- Optimiser les flux des processus afin de réduire les délais de livraison
- Impliquer l’ensemble des collaborateurs
- Miser sur un programme d’amélioration continue
À l’origine, le lean management a été déployé dans l’industrie automobile. Très rapidement, ce modèle de gestion s’est étendu à d’autres secteurs. Dans toutes les entreprises qui utilisent le lean management, l’accent est particulièrement mis sur :
- Le travail en équipe,
- La communication,
- L’utilisation efficiente des ressources,
- Et l’élimination des gaspillages.
Il s’agit ainsi de proposer un travail hautement qualifié dans des conditions idéales de fonctionnement, en minimisant les délais, les ressources et l’énergie nécessaires. À travers le lean management, la volonté est finalement d’apporter plus de valeur au client tout en éliminant les activités qui n’en ont pas.
Les nombreux outils du lean management
La méthode Kanban
Il s’agit d’une méthode née en tant que système de planification pour la fabrication lean. En japonais, “kanban” signifie “tableau visuel” ou “signe”. Les principales caractéristiques de cette méthode sont essentiellement les tableaux et les cartes.
La méthode 5S
Nous parlons d’une méthode allégée d’optimisation de l’espace de travail avec 5 étapes consécutives. Elles permettent aux équipes d’organiser leur lieu de travail pour une efficacité maximale des processus.
Ainsi, les 5 S sont issus de termes japonais suivants :
- “Seiri” (trier),
- “Seiton” (mettre en ordre),
- “Seiso” (briller),
- “Seiketsu” (standardiser),
- et “Shitruke” (maintenir).
La méthode Value Stream Mapping (VSM)
Le VSM offre, quant à lui, une cartographie de la chaîne de valeur. Il se présente comme un outil de gestion aidant les entreprises à visualiser, à analyser et à prendre les mesures qui s’imposent pour améliorer les étapes critiques d’un processus de livraison de produits.
SMED, Gemba Walk, Andon, Six Sigma, Muda, Just-in-Time (ou Juste-à-temps)… les outils du lean management sont nombreux et suivent tous une même ambition : servir les performances de l’entreprise. Ajoutons à ce stade, une citation de Cédric Bourgain, Responsable pédagogique sur le lean management chez CentraleSupélec : « On ne doit pas résumer le lean management à une liste successive d’outils, mais à une démarche continue ».
Le lean management : une méthode née par nécessité
Le lean management a fait son apparition au Japon, devenant la méthode de production Toyota par excellence. Après la Seconde Guerre mondiale, les constructeurs automobiles japonais se sont vus confrontés à un défi de taille. Il s’agissait de faire face à la montée en puissance des constructeurs automobiles occidentaux dont les chaînes de montage permettaient une production d’automobiles rapide et peu coûteuse. À l’époque, les méthodes de production archaïques des Japonais empêchaient les constructeurs de rivaliser en termes de coûts et de délais. Appauvris par la guerre, ils faisaient face à l’incapacité de financer de grandes quantités d’équipements ou de fournitures modernes et de haute technologie. Ils ont donc développé des solutions alternatives. Plutôt que d’investir dans de nouvelles machines, Toyota s’est ainsi concentré sur l’amélioration des processus de production, des flux de matériaux et des flux d’informations.
C’est ainsi qu’est né le système de production Toyota (TPS). Une solution permettant de produire des biens de qualité, au coût le plus bas et dans des délais d’exécution plus rapides. Pour atteindre ces objectifs, le TPS lutte en permanence contre les « Muda » (gaspillage), les « Mura » (déséquilibre) et les « Muri » (surcharge).
L’un des plus grands principes de management du 20e siècle est ainsi né pendant une période de crise. L’ingéniosité de la méthode permet finalement de se concentrer sur ce qui est déjà en place pour en tirer pleinement parti. C’est pour cela que l’on dit que le lean management considère toute crise comme une opportunité.
Un modèle toujours d’actualité
Certes, le lean n’est pas la théorie organisationnelle la plus récente qui soit. Néanmoins, elle peut être considérée comme étant toujours d’actualité. À y regarder de près, le lean management est particulièrement en phase avec le climat de crise économique et énergétique actuel. Les entreprises, quels que soient leur secteur d’activité et leur taille, doivent aujourd’hui faire preuve d’innovation dans leur approche de la résolution des problèmes. Pour traverser les crises, il leur faut s’adapter rapidement aux nouvelles situations et aux obstacles. Un seul dirigeant ne peut y parvenir seul. Il faut la contribution de toute l’équipe pour mener une mission à bien. Ce collectif doit réfléchir de manière créative, sans hésiter à revoir certaines croyances anciennes en vue de les améliorer.
La production de biens et de services de qualité au coût le plus bas et dans des courts délais est plus importante en période de ralentissement économique qu’en période d’expansion. L’entreprise peut ainsi recourir au lean management pour redresser une situation en période difficile. Bien au-delà des outils et des méthodes du lean, il s’agit de transformer l’état d’esprit de l’ensemble de l’organisation pour engager chaque collaborateur dans une démarche de résolution de problème. Les obstacles ne sont donc pas évités. Ils sont mis à profit pour que l’entreprise s’améliore. Ainsi, le lean management peut ainsi être considéré comme une méthode de transformation des organisations.
Le lean management : un modèle tout à fait adapté en temps de crise
Certains dirigeants d’entreprises envisagent l’introduction du lean management en période de stabilité et de constance. C’est lorsque des imprévus se présentent qu’ils recourent à des solutions de gestion de crise, dont le management de transition par exemple.
Pourtant, il existe une synergie entre la gestion de crise et le lean management. Les deux approches partagent des points communs. En effet, les principes fondamentaux du lean, présentés ci-dessus, sont similaires aux mesures que prennent les entreprises en période de crise pour maintenir leurs opérations et leur activité. Les exemples ci-dessous illustrent ceci.
Le personnel de l’entreprise est considéré comme la principale ressource
Dans le lean management comme dans la gestion de crise, n’est-il pas de rigueur de recourir à des spécialistes ? À des personnes dotées de qualifications et de connaissances particulières, pour travailler en équipe et résoudre les problèmes ? Ne compte-t-on pas sur le respect mutuel lors du travail en équipe ? Le dirigeant n’encourage-t-il pas chacun à proposer une solution, indépendamment de la fonction qu’il exerce ?
La réduction des coûts est un objectif primordial
Dans l’approche lean, on cherche à éliminer les pertes, à maintenir les stocks à un niveau minimum et à ajouter de la valeur au cours du processus. En situation de crise, l’entreprise ne cherche-t-elle pas à se montrer flexible et à utiliser les ressources disponibles ? N’a-t-elle pas intérêt à minimiser le gaspillage et à se défaire des procédures bureaucratiques qui n’apportent aucune valeur ajoutée aux processus ?
Le management visuel et l’ordre
Dans l’approche lean, les outils de gestion visuelle permettent de tenir les salariés au courant des dernières actions menées. L’accent, à l’instar du système 5S, est avant tout mis sur la propreté et l’organisation de l’ensemble de la production, jusqu’à chacun des postes de travail. En situation de crise, la rapidité avec laquelle les décisions critiques doivent être prises ne repose-t-elle pas sur l’accès immédiat à des données organisées, accessibles à tous et à tout moment ?
Si le lean management puise ses origines au milieu du 20e siècle, il n’en reste pas moins une méthode de gestion actuelle, en phase avec les besoins de l’entreprise en période de crise. Loin d’être dépassé, le lean management est une méthode rattrapée par le temps et par les événements qui façonnent le monde de demain.